How to Choose the Best Rubber Sheets for Your Specific Needs
Rubber sheets are widely used in various industries, ranging from automotive to construction, food processing to manufacturing. With so many types of rubber available, it can be challenging to know which one is right for your specific needs. Whether you’re working on a DIY project, designing a new product, or replacing old rubber sheets, it’s essential to understand the different types and characteristics of rubber to make the best choice. In this blog, we’ll guide you through the process of selecting the best rubber sheets for your specific requirements, ensuring that you make an informed decision every time.
What Are Rubber Sheets?
Before we dive into how to choose the best rubber sheets, let’s first understand what they are and how they are used.
Rubber sheets are flat pieces of rubber that come in different thicknesses, sizes, and grades. They are often used as a sealing material, insulation, or protection against damage. Rubber sheets are also used in gaskets, flooring, vibration dampening, and other industrial applications.
There are several types of rubber used in these sheets, each with its unique set of properties. The most common types are natural rubber, neoprene, EPDM, nitrile, and silicone. The right choice depends on factors like temperature tolerance, chemical resistance, flexibility, and durability.
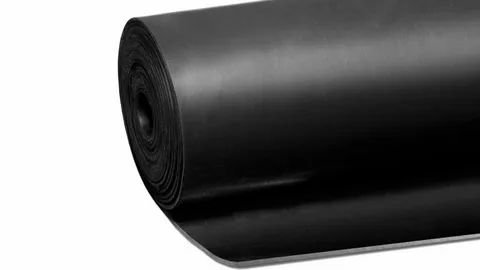
Why Are Rubber Sheets Important?
Rubber sheets serve a variety of purposes, and understanding their importance in your project or application is crucial. Let’s explore some reasons why they are widely used:
1. Protection
Rubber sheets act as a protective barrier against various elements, including moisture, chemicals, and physical abrasion. They are often used to line surfaces or to create seals, preventing wear and tear.
2. Durability
The materials used in rubber sheets are designed to last a long time. They can withstand harsh conditions, making them ideal for use in industrial environments or other demanding applications.
3. Flexibility and Versatility
Rubber sheets are highly flexible, which makes them adaptable for various uses. Whether you need to use them as seals, flooring, or vibration dampers, rubber sheets can meet your specific needs.
4. Cost-Effective
Compared to other materials, rubber is often a more affordable option, especially when used for large-scale industrial applications. Its long-lasting properties can also help save money in the long run.
How to Choose the Best Rubber Sheets for Your Specific Needs?
When choosing rubber sheets for your specific needs, you should consider several factors that will impact performance. Here are some key points to keep in mind:
1. Consider the Type of Rubber
The type of rubber you choose is critical because each type has different properties that make it suitable for specific applications. Let’s look at the most common types of rubber used in rubber sheets:
Natural Rubber
Natural rubber, also known as latex rubber, is a flexible material that offers excellent resistance to wear and tear. It’s often used in applications that require flexibility, such as in gaskets, seals, and vibration dampening. However, it is not suitable for high temperatures or exposure to oils and chemicals.
Neoprene Rubber
Neoprene is a synthetic rubber that offers good chemical resistance, temperature tolerance, and durability. It’s often used in automotive and industrial applications where exposure to oils, fats, and chemicals is common. Neoprene rubber sheets are ideal for sealing, insulation, and soundproofing.
EPDM Rubber
EPDM (ethylene propylene diene monomer) rubber is known for its excellent resistance to weather, UV light, and ozone. It’s commonly used in outdoor applications, such as roofing, automotive weather seals, and agricultural systems. EPDM rubber sheets are ideal for use in environments where exposure to the elements is a concern.
Nitrile Rubber
Nitrile rubber, also known as Buna-N, is highly resistant to oils, fuels, and solvents. It’s often used in applications like automotive seals, fuel gaskets, and O-rings. Nitrile rubber sheets are ideal for environments where there is exposure to oils, grease, and petroleum-based products.
Silicone Rubber
Silicone rubber is well-known for its ability to withstand high temperatures, making it ideal for applications in industries such as food processing, electronics, and medical. Silicone rubber sheets are highly flexible and durable, and they perform well in both hot and cold environments.
2. Thickness and Size
The thickness and size of the rubber sheet are also crucial factors to consider. The thickness of the rubber sheet will determine its flexibility, durability, and strength. Here’s a general guideline for selecting the right thickness:
- Thin Rubber Sheets (less than 1/8 inch) are ideal for applications like gasketing, sealing, and cushioning.
- Medium Thickness Rubber Sheets (1/8 inch to 1/4 inch) are typically used for vibration dampening and general-purpose seals.
- Thick Rubber Sheets (more than 1/4 inch) are best for heavy-duty applications such as impact protection, anti-slip surfaces, and industrial use.
The size of the rubber sheet will depend on the specific dimensions of the area you plan to cover. Rubber sheets can usually be purchased in rolls or pre-cut sizes, but you can also have them custom-cut to fit your exact needs.
3. Temperature Resistance
Different rubber materials have different temperature ranges. If your application involves high temperatures, such as in industrial machinery or automotive engines, it’s crucial to choose a rubber that can withstand those conditions. Silicone rubber, for example, is excellent for high-temperature applications, while EPDM performs well in both hot and cold environments.
If the application involves freezing or extremely low temperatures, materials like neoprene or nitrile rubber might be better suited as they offer good cold-weather resistance.
4. Chemical Resistance
If the rubber sheet will be exposed to chemicals, oils, or solvents, chemical resistance is a critical consideration. Nitrile rubber, for example, is highly resistant to oils, while neoprene is resistant to chemicals like gasoline, fuel, and certain acids. Be sure to choose a rubber type that can withstand the specific chemicals your product or application may encounter.
5. Flexibility and Compression Set
Flexibility and the ability to return to its original shape after compression are essential factors for certain applications. A rubber sheet that’s too stiff might not work well for gaskets or seals. On the other hand, a rubber sheet that’s too soft might wear out more quickly.
Check the compression set of the rubber—this is a measure of how well it recovers after being compressed. A low compression set indicates that the rubber will return to its original shape after being pressed, which is ideal for seals and gaskets.
6. Durability and Wear Resistance
Durability is a significant factor for rubber sheets, especially in industrial applications where the material will face constant wear. Materials like natural rubber are durable and resistant to abrasion, but they may not last as long as synthetic rubber types in harsh conditions. Neoprene and nitrile offer superior durability and are well-suited for demanding environments.
If your application involves heavy machinery or constant friction, choose rubber sheets with high wear resistance to prevent frequent replacements.
7. Cost
Cost is always an important consideration when purchasing materials for a project. While natural rubber is generally more affordable than synthetic rubbers, it may not perform as well in certain applications. You’ll need to balance the material’s cost with its performance and longevity to find the best option within your budget.
While synthetic rubbers like silicone and nitrile are more expensive, they offer enhanced performance for specific needs, so they might be worth the investment if your project demands higher quality.
Where to Use Rubber Sheets?
Once you’ve considered all the factors above, it’s essential to know where you can use rubber sheets. Rubber sheets are versatile and can be used in many applications, including:
- Gaskets and Seals: For industrial machinery, automotive parts, and appliances.
- Flooring: In commercial and residential spaces to reduce noise, provide insulation, or prevent slip hazards.
- Vibration Dampening: In machinery or vehicles to reduce noise and prevent damage from vibrations.
- Packaging and Protection: To protect items during transport or as liners for containers.
- Food Processing: In environments where hygiene is critical, such as in food manufacturing and packaging.
Conclusion
Choosing the best rubber sheets for your specific needs doesn’t have to be overwhelming. By considering factors such as rubber type, thickness, temperature resistance, chemical resistance, flexibility, durability, and cost, you can make an informed decision that will benefit your project in the long run. Whether you’re working in automotive, industrial, or food processing industries, the right rubber sheet will help ensure durability, efficiency, and performance. Always remember to choose a reliable supplier that offers high-quality rubber sheets suited to your needs.
With this guide, you now have all the necessary information to select the perfect rubber sheet for your specific requirements. Whether it’s for DIY projects, industrial use, or machinery parts, make sure you pick the right material to get the best results.